- InverterTop
- Inverter
- Inverter options (peripheral devices)
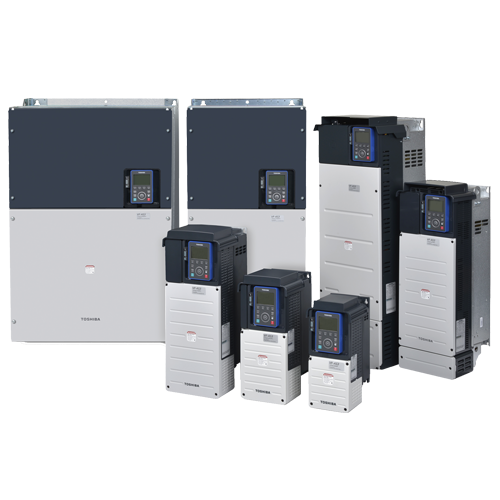
High-performance inverter VF-AS3
This series is the highest drive performance and the most functions among the Toshiba inverter series inverters. It can be used for a vast range of applications.
High-performance inverter VF-AS3
About High-performance inverter VF-AS3
For plant and equipment applications, the inverter has the STO (Safe Torque Off) function compliant with the relevant safety standards to cut off the output with high reliability in an emergency.
Input voltage class/applicable motor capacity
[HD ratings]
・Three phase 240 V input: 0.4 to 55 kW
・Three-phase 480 V input: 0.4 to 280 kW
・Three-phase 500 V input: 1.5 to 55 kW
・Three-phase 600 V (575 V) input: 2.0 to 75 HP
・Three-phase 690 V input: 2.2 to 75 kW
・Three-phase 480 V input: 0.4 to 75 kW (IP55)
[ND ratings]
・Three-phase 240 V input: 0.75 to 75 kW
・Three-phase 400 V input: 0.75 to 315 kW
・Three-phase 500 V input: 2.2 to 75 kW
・Three-phase 600 V (575 V) input: 3.0 to 100 HP
・Three-phase 690 V input: 4.0 to 90 kW
・Three-phase 480 V input: 0.75 to 90 kW (IP55)
Features
- Double ratings (HD ratings/ND ratings)
- A rich set of functions for plant and equipment applications
- The inverter has an LCD operation panel with a large screen as a standard feature.
Double ratings (HD ratings/ND ratings)
HD (Heavy Duty) ratings
(Equivalent to VF-AS1)
・Constant torque applications
・Current overload capacity: 150% for 1 minute
・Applications: Conveyors, cranes, etc.
ND (Normal Duty) ratings
(Equivalent to VF-PS1)
・Reduced load torque applications
・Current overload capacity: 120% for 1 minute
・Applications: Fans, pumps, etc.
A rich set of functions for plant and equipment applications
PM motor control
The inverter can drive both IPM and SPM motors. Sensor-equipped and sensor-less models are both supported.
Droop control (load sharing)
When multiple inverters and motors operate a single load, this function prevents the load from concentrating on a specific motor due to the load imbalance.
The inverter has an LCD operation panel with a large screen as a standard feature.
Large LCD screen
The screen can display various types of information (9 languages).
If a trip occurs, the backlight color changes to red to alert the user.
QR code®/video guidance
The QR code® shown on the screen lets you access video-based operation instructions or a description of the action to take in the event of a trip.
Parameter writer function
This function allows you to save and copy the parameters.
Adopts
- Improved environmental durability
- Long-life design offering an expected design life of as many as 10 years
- Reducing PLCs leads to space and cost savings.
- Reduction in the adjustment time
- Reduction in maintenance costs
Improved environmental durability
Comply with the chemicals (3C3)/dust (3S3) standards of IEC60721-3-3. (Frame size A6 or smaller)
The inverter is operable at an ambient temperature of -15 to +60°C. (Frame size A7 and A8: -10 to 60°C)
Long-life design offering an expected design life of as many as 10 years
The use of a long-life cooling fan (*1), main circuit capacitor and control board capacitor enables long-life design offering an expected design life of as many as 10 years (*2).
(*1) 5 years for the cooling fans of frame size A7 and A8
(*2) Annual average ambient temperature: 40°C; output current: 80% of the rated current; relative humidity: 65%; when remaining in operation 24 hours a day, 365 days a year. The expected design life is a calculated value, not a guaranteed value.
Reducing PLCs leads to space and cost savings.
- Four-PID control function
The inverter has two PID controls for driving the motor and another two independent PID controls, making it possible to also control the peripheral devices, such as valves and heaters, simultaneously. - Multi-pump function
The function can control up to 10 pump motors (extension terminal box option) in terms of the flow rate, pressure, keeping the temperature constant, etc. - Calendar function
The real-time clock (RTC), which manages the year, month, day of month, day of week and hour data, allows you to start or stop the operation at a specified time. - My Function
The My Function built in the inverter handles part of the external circuit consisting of relays, PLC and other components to simplify the system.
Reduction in the adjustment time
You can auto-tune the motor constants, set the load inertia moment automatically, adjust the PID gains automatically and set the braking and light-load high-speed operation functions of a lifting machine automatically, among other things. This enables optimum adjustment and a reduction in the adjustment time.
Reduction in maintenance costs
Remote monitoring using the Ethernet communication, which is supported as a standard feature, eliminates the need for on-site checks and operations.
The operation status of the peripheral devices can also be monitored remotely by connecting a sensor to the inverter and using the inverter as an IoT terminal.
Performance
- Energy-saving effect and CO2 reduction
- Suppression of harmonics and improvement in the power factor
- Easy replacement from the existing VF-AS1 model
- Capable of cutting off the output in compliance with safety standards
Energy-saving effect and CO2 reduction
When the inverter controls the air volume and flow rate of the general fans and pumps, the shaft power lowers, which saves energy.
Suppression of harmonics and improvement in the power factor
The built-in or optional DC reactor suppresses harmonics while improving the power factor. Also, since the input current becomes small, this design is friendly to the power system and peripheral devices.
・An input power factor over 94%, specified in the Standard Specifications for. Public Works Construction (2019 Edition) supervised by the Ministry of Land, Infrastructure, Transport and Tourism, has been achieved.
(The input rector and DC reactor are required.)
・Built-in/attached DC reactor as a standard feature.
Easy replacement from the existing VF-AS1 model
・The installation dimensions are compatible.
・The parameters*1 set for the existing models VF-AS1 and VF-PS1 can be converted easily to the VF-AS3 parameters by using a dedicated tool.
*1: Reading the parameters from VF-AS1 or VF-PS1 requires the USB001Z option.
Capable of cutting off the output in compliance with safety standards
The inverter features the STO (Safe Torque Off) function compliant with the relevant safety standards and can cut off the output with high reliability in an emergency. The STO function reduces the motor torque close to zero in a safe manner and controls the motor to prevent it from starting inadvertently.
This function is compliant with the IEC61800-5-2 and IEC61508 SIL3 safety standards.
High-performance inverter VF-AS3 Spec
Item | VF-AS3 | ||
---|---|---|---|
Rating | Applicable motor (kW) HD(Heavy Duty) rating | 3-phase 240V input class | 0.4 to 55kW |
3-phase 480V input class | 0.4 to 280kW | ||
3-phase 500V input class | 1.5 to 55kW | ||
3-phase 600(575)V input class | 2.0 to 75HP | ||
3-phase 690V input class | 2.2 to 75kW | ||
3-phase 480V input class (IP55) | 0.4 to 75kW | ||
Applicable motor (kW) ND(Normal Duty) rating | 3-phase 240V input class | 0.75 to 75kW | |
3-phase 480V input class | 0.75 to 315kW | ||
3-phase 500V input class | 2.2 to 75kW | ||
3-phase 600(575)V input class | 3.0 to 100HP | ||
3-phase 690V input class | 3.0 to 90kW | ||
3-phase 480V input class (IP55) | 0.75 to 90kW | ||
Overload current rating (HD rating) | 150% - 1 minute | ||
Overload current rating (ND rating) | 120% - 1 minute | ||
Dynamic braking circuit | Embedded / option *A | ||
Power supply (Voltage - frequency) | 3-phase 240V input class | 3-phase 200V to 240V, 50/60Hz | |
3-phase 480V input class | (VFAS3-4004PC to 4132KPC, 4004PCE to 4750PCE) 3-phase 380V to 480V, 50/60Hz | ||
(VFAS3-4160KPC to 4280KPC) 3-phase 380V to 440V, 50Hz 3-phase 380V to 480V, 60Hz | |||
3-phase 500V input class | 3-phase 500 V to 690 V - 50/60 Hz | ||
3-phase 600(575)V input class | 3-phase 500 V to 600 V - 50/60 Hz | ||
3-phase 690V input class | 3-phase 500 V to 690 V - 50/60 Hz | ||
Power supply (Allowable fluctuation) | Voltage: -15%, +10%, frequency: +/-5% | ||
Degree of protection (IEC60529) | IP20 / IP00 / IP55 *C | ||
Cooling method | Forced air-cooled | ||
EMC filter (IEC61800-3) | Embedded (400V, 500/600/690V input model) | ||
DC reactor | Embedded / attached DC reactor *B | ||
Control specifications | Output frequency range | 0.01 to 590Hz | |
Minimum setting steps of frequency | 11 bits | ||
Frequency accuracy | Analogue | +/-0.2% of the maximum output frequency | |
Digital | +/-0.01% +/-0.022 Hz of the output frequency | ||
Voltage/frequency characteristics | V/f constant, Variable torque, Automatic torque boost, Sensorless vector control, Energy savings, Dynamic energy savings, PM motor control, V/f 5-point setting, PG feedback control, PG feedback vector control, PG feedback PM motor control | ||
Interface specifications | Digital input | 14 (6: option) | |
Digital output | 3 (2: option) | ||
Pulse train frequency input | 2 (selectable PTI / digital input) | ||
Pulse train frequency output | 1 (selectable PTO / digital output) | ||
Relay output | 1c, 5a (3a: option) | ||
Analogue input | 5 (2: option) | ||
Analogue output | 2 | ||
PTC input | 3 (1: PTC/AI, 2: option) | ||
Control power supply | Output | 10Vdc - 10mA | |
24Vdc - 200mA | |||
Input | 24Vdc - 1A | ||
Functional safety | Safe Torque Off comply with IEC61800-5-2 (Dual port) | ||
Communication | Embedded | RS485: 2 channel (Toshiba inerter protocol, Modbus RTU) | |
Ethernet: Dual port with switch (EtherNet/IP, Modbus TCP) | |||
Option | DeviceNet | ||
PROFIBUS DP | |||
EtherCAT | |||
PROFINET | |||
CANopen | |||
Environment | Ambient temperature | -10 to +60 °C *1 | |
Storage temperature | -25 to +70 °C (Temperature applicable for a short term.) | ||
Relative humidity | 5 to 95% (free from condensation) | ||
Altitude | 4800m or less *2 *3 | ||
Vibration | 5.9m/s2 (0.6G) or less (10 to 55Hz) *4 |
*1: Need current reduction above 50 °C
[IP55] -10 to +50 °C (Need current reduction above 40 °C)
*2: Need current reduction over 1000m
*3: Depends on earthing system
*4: Frame size A7, A8: 2.9m/s2 (0.3G) or less (10 to 55Hz)
*A Embedded braking circuit except the following models. VFAS3-4132KPC (Need PB7-4132K and braking resistor) VFAS3-4220KPC to 4280KPC (Need PB7-4200K and braking resistor) |
*B Embedded: VFAS3-2004P to 2550P, 4004PC to 4132KPC Attached DC reactor:VFAS3-4004PCE to 4750PCE VFAS3-6022PC to 6750PC VFAS3-4160KPC to 4280KPC |
*C IP20: VFAS3-2004P to 2370P, 4004PC to 4750PC IP00:VFAS3-2450P, 2550P, 4900PC to 4280KPC IP55:VFAS3-6022PC to 6750PC VFAS3-4004PCE to 4750PCE |
Input voltage classes and applicable motor capacity range
[HD ratings]
Three phase 240 V input: 0.4 to 55 kW
Three-phase 480 V input: 0.4 to 280 kW
Three-phase 500 V input: 1.5 to 55 kW
Three-phase 600 V (575 V) input: 2.0 to 75 HP
Three-phase 690 V input: 2.2 to 75 kW
Three-phase 480 V input: 0.4 to 75 kW (IP55)
[ND ratings]
Three-phase 240 V input: 0.75 to 75 kW
Three-phase 480 V input: 0.75 to 315 kW
Three-phase 500 V input: 2.2 to 75 kW
Three-phase 600 V (575 V) input: 3.0 to 100 HP
Three-phase 690 V input: 4.0 to 90 kW
Three-phase 480 V input: 0.75 to 90 kW (IP55)